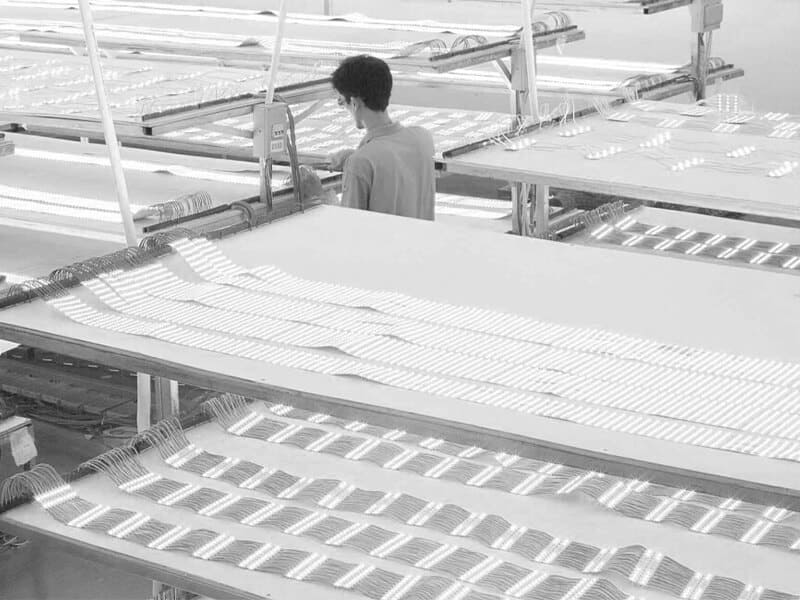
在 LED 柔性灯条的生产过程中,难免会出现一些问题。今天,笔者就来简单总结一下常见的问题。
一个在生产 LED 柔性灯条的过程中,胶水中会出现气泡。 主要原因是涂胶操作时间过长、涂胶量过大、混合方法不正确、没有真空脱气或脱气时间太短。
1.胶水操作时间过长:环氧 AB 胶水或聚氨酯胶水混合后放置的时间越长,胶水的粘度就会越来越稠。胶水变稠后,气泡将难以排出。解决方法:缩短操作时间(分为:点胶时间、抽真空时间、停放时间、点胶时的使用时间)。
2.用胶量:当环氧树脂胶或聚氨酯胶的环境温度恒定时,一次混合的胶量越大,固化速度越快。如果胶水用量过多,随着时间的推移,胶水的粘度会逐渐增大,胶水会变得越来越粘稠,气泡排出相对困难。解决办法:建议少用一点胶水,200G/200G 比较合适。如果要多搅拌,建议搅拌均匀后将胶水分成 2-4 杯,进行消泡和抽真空(原理:体积越大,固化速度越快)。如果不分割,胶水的粘度会在短时间内变稠。最后,气泡难以排出。
3.搅拌方法不正确:解决办法是顺时针搅拌。因为顺时针搅拌和逆时针搅拌更容易产生气泡。
4.一定要脱泡(真空机),建议脱泡时间为 6-8 分钟。
二。LED 柔性灯条生产过程中,胶水表面不干。主要原因是胶水配比不准确或搅拌不够均匀。
1.胶水比例不准确:比例不准确时,部分胶水不能发生化学反应,如果不发生反应,就不能完全固化,所以不会干,也不会很粘。解决办法:胶水混合的误差范围应控制在 1%-1.5% 之间。
2.胶水混合不均匀:搅拌不均匀会导致表面干燥、部分干燥或固化时间变长。解决办法:在搅拌过程中,要确保容器周围和底部搅拌到位。建议搅拌时间为 5-6 分钟。
三、胶水固化后的现象和解释胶水固化后的现象和解释。
1.环氧树脂胶长时间放在水中,表面会变白,但取出后在室温下放置 5 小时即可恢复原状。聚氨酯胶放在水中不易变白。
2.关于胶水、硅胶和 PVC 的粘接性能:硅胶材料和 PVC 是很难粘接的材料。环氧树脂胶水对 PVC 有一定的粘结力,但与硅胶材料的粘结性能不好,与硅胶 U 形套管粘结时容易断裂。
3.胶水基本固化后,表面看起来会有点粘手,所以不要在 24 小时后再辘辘包装。如果 24 小时后再包装,表面容易粘手,也容易破损,因为 24 小时后,胶水处于基本固化状态,还没有完全固化。解决方案:建议在 48 小时后进行收卷和包装。
4.灯带 SMD 灯管上的胶水开裂的主要原因是:胶水混合不准确或混合不均匀,导致胶水固化不完全,以及灯带表面涂层不足。