It’s quite common that LED strips stops working after being cut, especially for those people who dose not have much experience on DIY. On the condition that the strips do work before cutting, here are the potential causes and solutions.
Parts of LED strip is not working
1. Incorrect cutting point
Cause: Flexible LED strips is cuttable, usually the cutting points is marked by a line or a scissor icon. Cutting the strip at any point other than the designed points can break the circuit, which causes this unit of the strip not working.
Solution: Cut off this damaged unit at correct cutting point, expand another unit on strip by soldering or solderless connectors if needed.
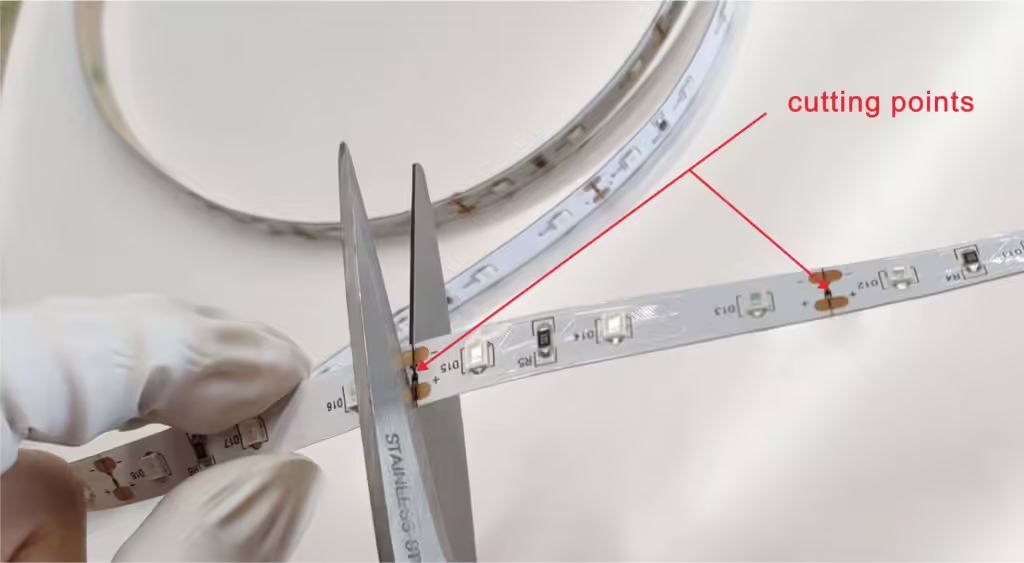
2. Electrostatic damage
Cause: Static electricity creates high-voltage spike which easily breakdown LED chip’s P-N junction, it happens by touching soldering pad or LED chips directly.
Solution: Put on anti-static wrist strap before cutting, other static elimination works as well.
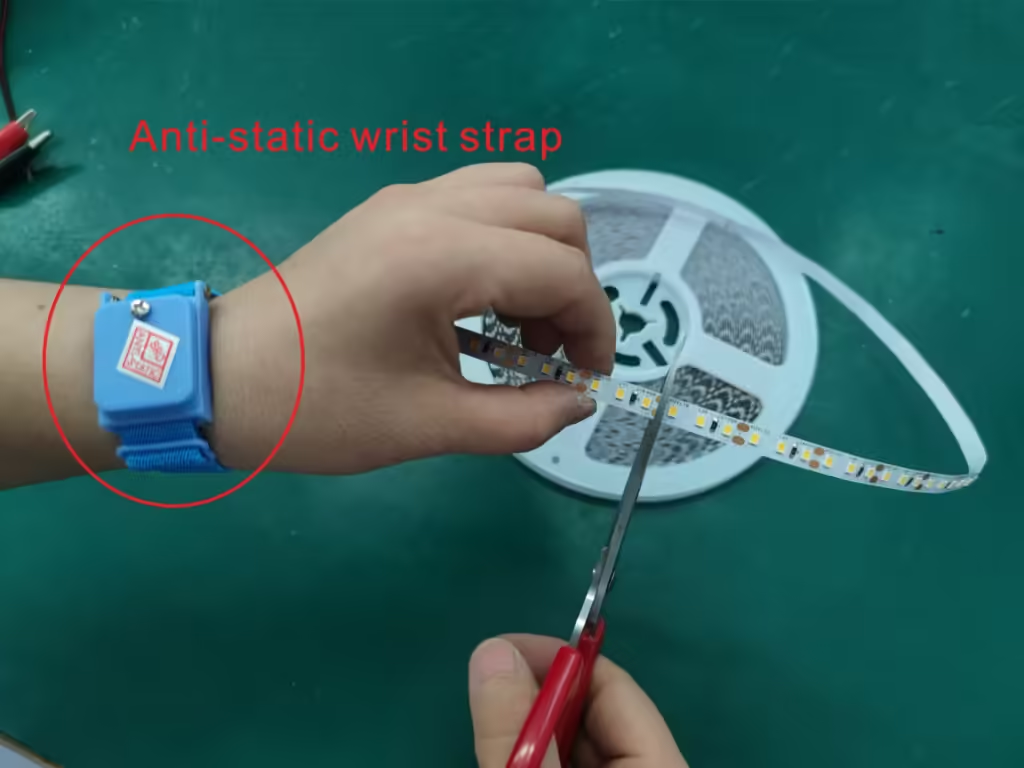
3. Connection issue
Cause: When connect two strips together after cutting, faulty soldering or bad connection by solderless connectors leads to the following strips not working.
Solution: Inspect the solder joints, re-solder the weak joints; Replace connectors, ensure it fits well and tight.
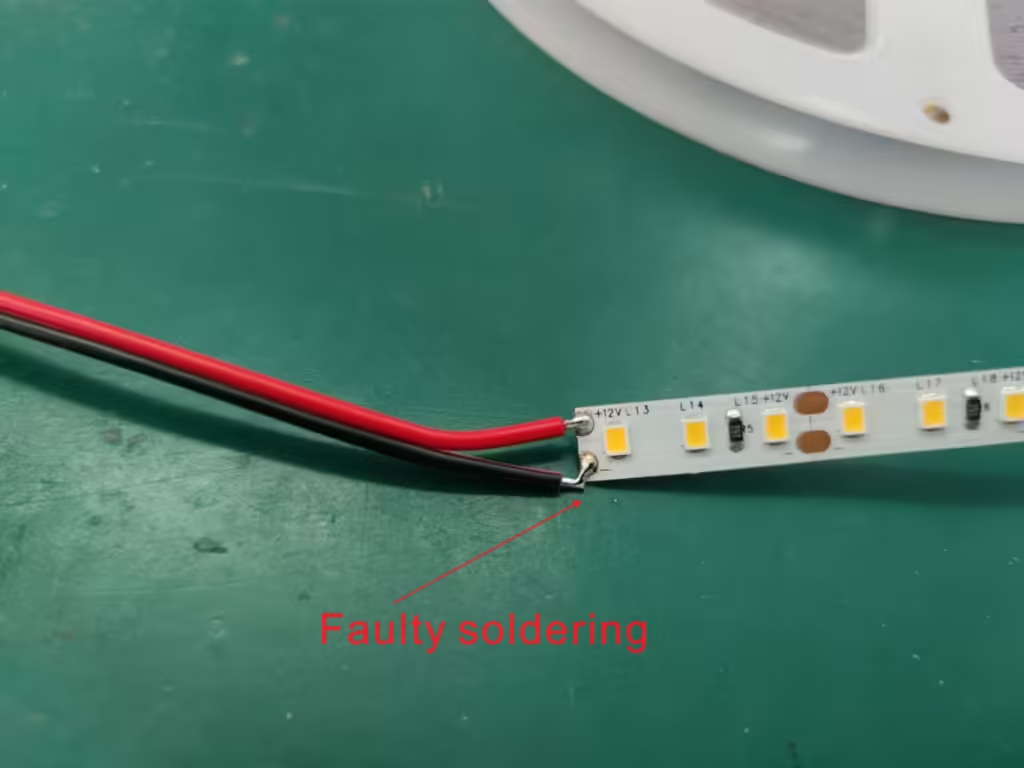
Entire LED strip is not working
1. Short circuit
Cause: Forget to turn off the power while cutting the strips or solder positive and negative polarity together accidentally, this short circuit creates surge current which burns LED chips;
Solution: Disconnect strips to LED driver before cutting; Check if there is any soldered joints problem.
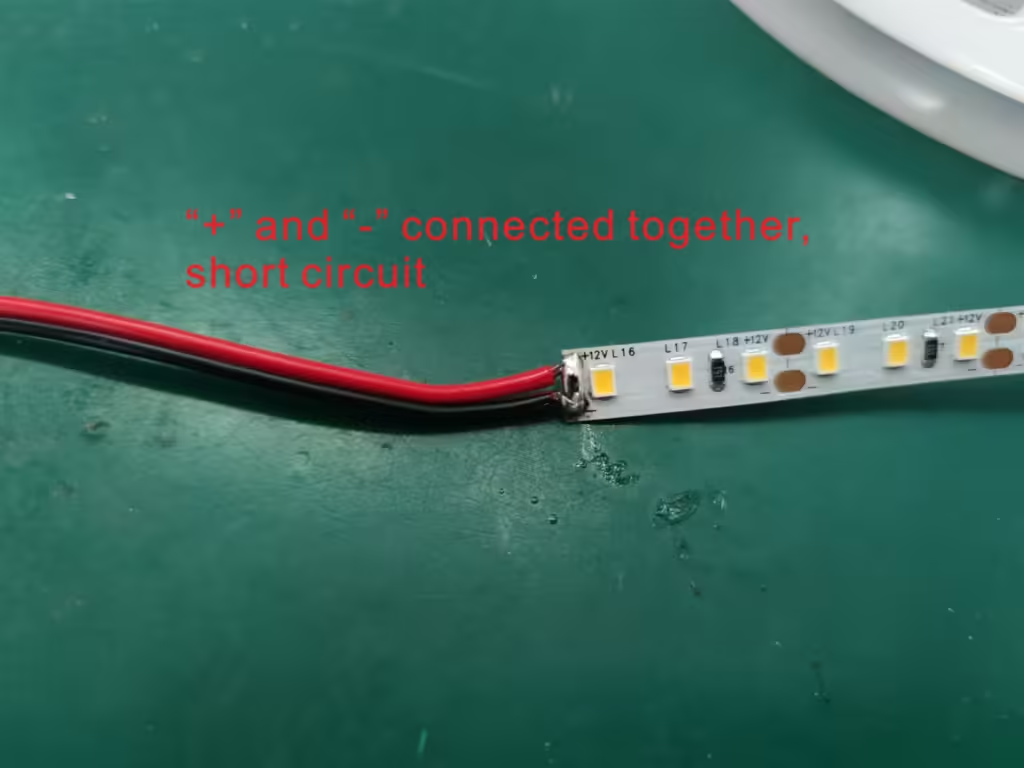
2. Polarity Reversal
Cause: a. Reversing the polarity when connect strips to LED driver.
b. Reversing the polarity when solder cable or use solderless connectors. Such as “+” and “-” mixed or “R”, “G”, ”B” and “+” mixed.
Solution: Double check polarity of cable and soldering joints before power on.
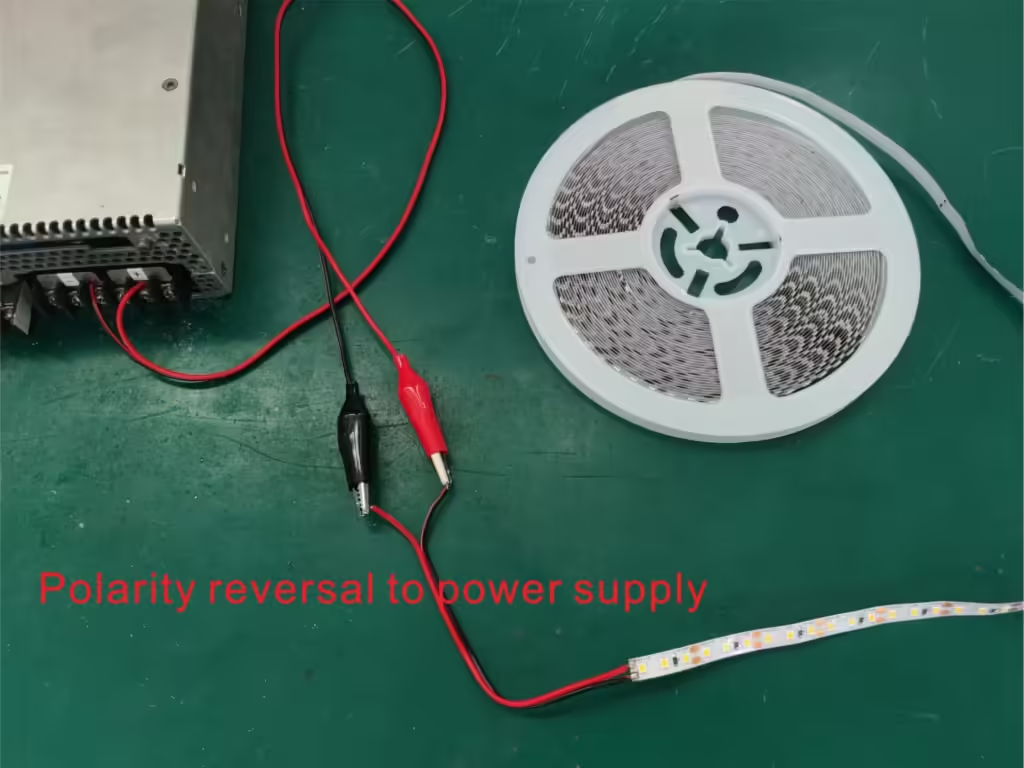
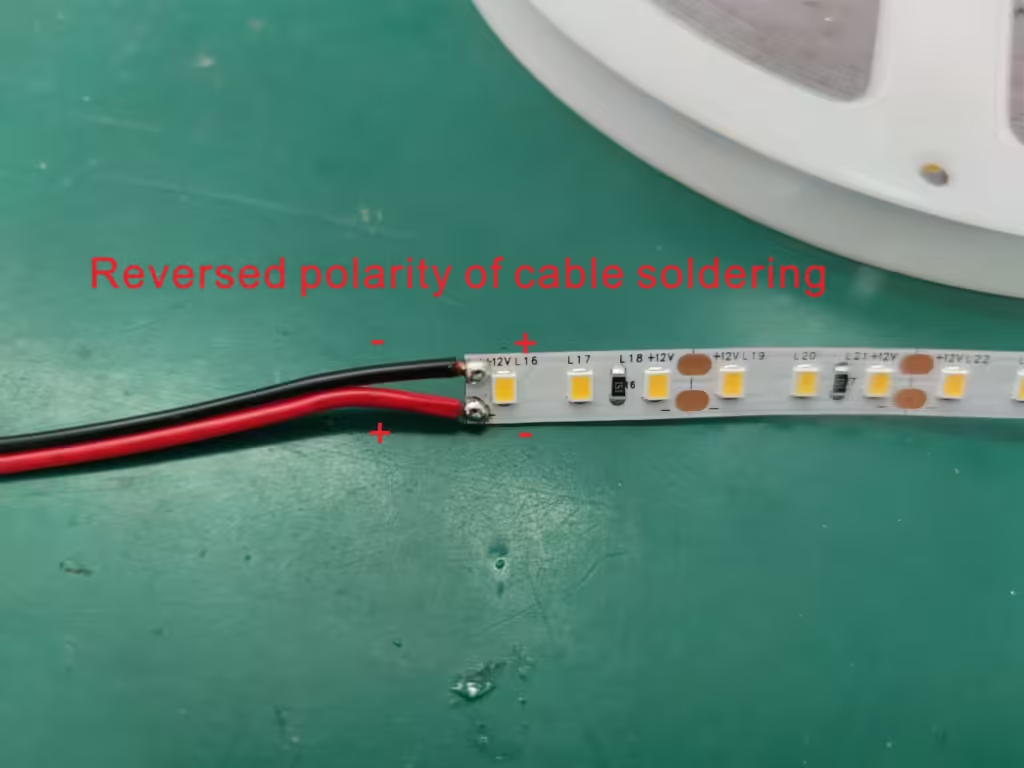
3. Connection issue
Cause: Cable is not soldered to strips well or connectors does not fit strips well may cause incomplete electric circuit
Solution: Make sure the connectors or soldered joints are properly aligned and securely attached to the copper pads. If using snap or solderless connectors, ensure they are compatible with the strip’s width and pin configuration.
4. Power supply issue
Cause: After cutting and reconnecting LED strips, the power supply might not provide adequate voltage or current, especially if the strip length has changed significantly.
Solution: Calculate how much power the new strip need, change power supply if the old one is not powerful enough.
Additional tips:
1. Disconnect power supply before cutting and reconnecting.
2. Check all the solder joints and other connections before power on.
3. Prepare some equipment, anti-static wrist strap for static elimination, multimeter for measuring voltage and current, checking if the solder joints is shorted.
4. Contact us for help.