There are various types of LED strip lights on the market, mainly classified according to the type of light source, use, installation scenario, control mode, and so on. LED lights can be divided into different models according to the type of light source, such as 5050, 2835, etc., and different packaging methods, such as COB and SMD. In addition, according to the use, there may be indoor, outdoor, decoration, lighting, and other different uses of the light belt. This article discusses with you the LED light strips often used in ordinary life.
Classification by voltage: can be divided into low voltage LED strip and high voltage LED strip.
What is a low voltage LED strip?
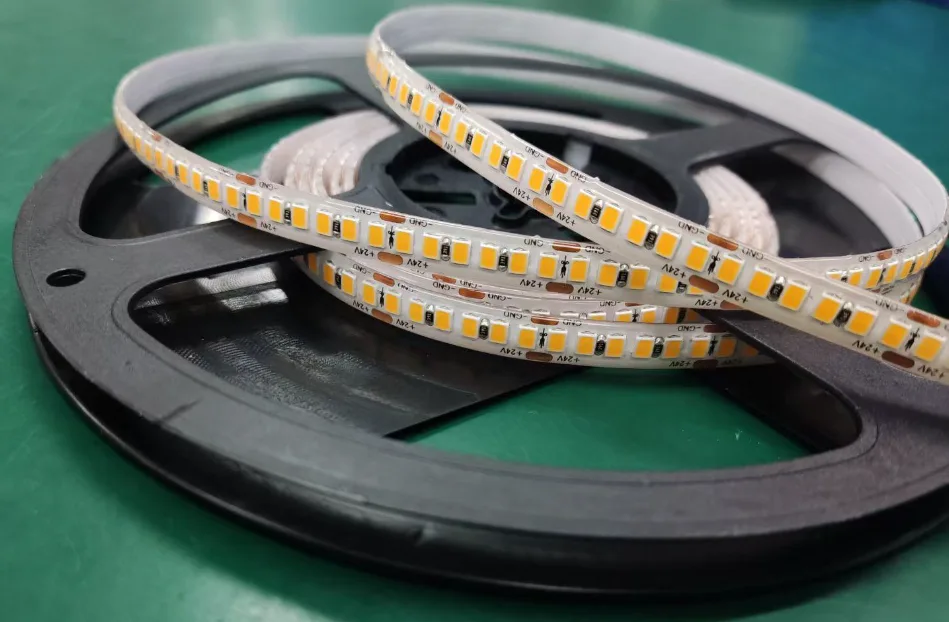
Low voltage LED strip by flexible circuit board, LED, resistance, and insulation packaging materials, low voltage LED strip is a low-voltage (12V/24V/5V) driven LED lighting product, low voltage LED strip safety, needs to be used with LED transformers, suitable for home or short-distance installation.
Key Features:
- Low voltage greatly reduces the risk of electric shock, especially suitable for humid environments (bathrooms, swimming pools) and children’s activity areas.
- It can be freely clipped (usually one cut every 3 lamp beads), bent to fit the shaped space, and the thickness is only 2-3 mm for hiding.
- 2700K-6500K color temperature options; high-end models support RGB full color changes, enabling flexible lighting solutions.
Applications:
Commercial space: Jewelry counter (12V/6W per meter) display lighting, clothing store changing mirror auxiliary light
Home scene: kitchen cabinet bottom light (24V waterproof), stair step light, bedroom contour light
Outdoor applications: IP67-grade products are used for garden path lighting and building facade outlines.
Compared with the high voltage LED strip (220V direct drive), the low voltage strip light requires additional transformers, but its safety and controllability make it the preferred solution for modern smart home lighting, especially in scenarios requiring frequent contact or complex installation.
What is a high voltage LED strip?
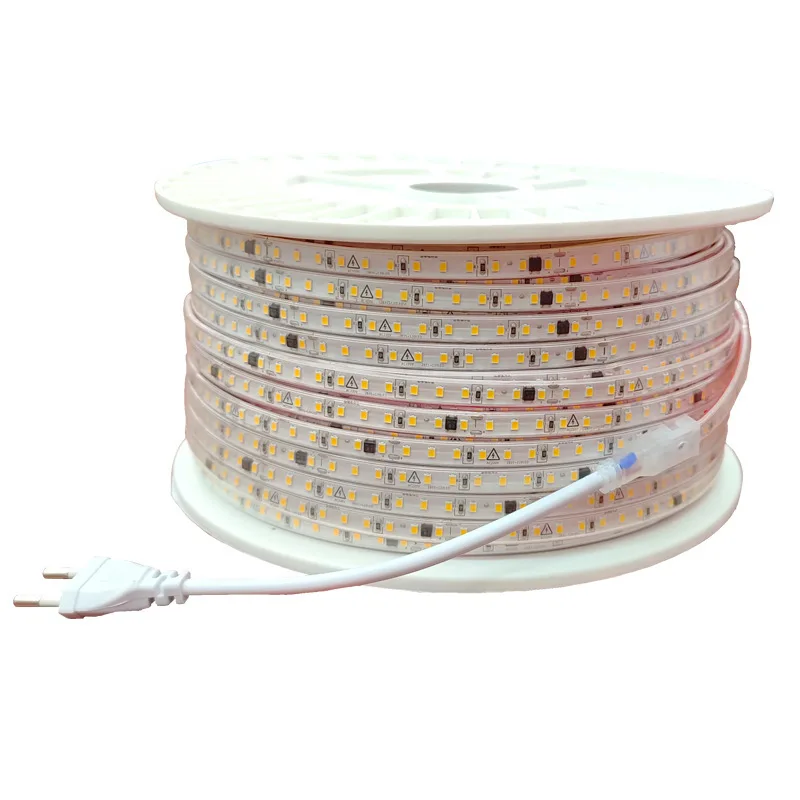
High voltage LED strip is a high-voltage (usually 110V-240V AC) LED lighting product, which can be directly connected to home or commercial electricity without additional transformers. Suitable for long-distance use, such as building profile lighting, outdoor decoration, and high voltage LED strip use, should pay attention to insulation protection.
Key Features:
- High voltage, low current Direct use of mains (such as 220V), small current, suitable for long-distance installation (single up to 50-100 meters), no obvious voltage drop problem
- Easy to install, no need for external transformers or drivers, saving installation costs and time, suitable for large areas or complex wiring scenarios.
- Lower cost, Compared with the low voltage LED strip, the transformer cost is eliminated, and the overall cost is lower.
Applications:
Commercial space: shop signs, exhibition hall decoration, building profile lighting, and other long-distance needs.
Home decoration: ceiling, background wall, and other areas to hide wire.
Outdoor scene: courtyard, landscape lighting, and other needs to be waterproof, weatherproof environment (need to select IP65 and above protection level).
High voltage VS Low voltage LED strip
Speciality | High Voltage LED Strip | Low Voltage LED Strip |
Voltage | 110V-240V AC | 5V/12V/24V DC |
Mounting distance | A single strip can reach 100 meters | Usually10-15 meters (approx) |
Safety | Need professional installation, prevent the risk of electric shock | Safer, suitable for human contact areas |
Cut mark length | 10 cm, 50cm | 5 cm to 10 cm |
IP rating | Usually, high IP ratings ranging from IP65 to IP68 | from IP20 to IP68 |
Lifetime | Generally around 10,000 hours | Longer service life of 30,000 -50,000 hours |
Packaging | Generally 50-100 meters per roll | Typically 5-10 meters per roll |
Applicable | Long distance, commercial, outdoor | Short distance, home, children’s room, etc |
The installation of the high voltage LED strip is simple and convenient; you only need to connect the mains, which can be used, and the installation is not limited by the distance, as it can be directly connected to the place 100 meters away. For large installations using low voltage LED strips, the voltage drops after the strip reaches a distance of 15-20 meters, and you will need multiple power supplies, which will increase the total cost. The upfront cost of low- and high-voltage LED strips is similar, but the overall price of high-voltage lines may be a little cheaper.
High voltage LED strips usually use linear power supplies, which will be worse in service life and stability than low-voltage lamp strips, and the use of low voltage LED strips is cost-effective in the long run. If you need a more secure solution or a short-distance decoration (such as cabinets or furniture), low voltage LED strips may be a better choice.
Is the high voltage LED strip brighter than the low voltage LED strip?
In fact, the brightness has little to do with the voltage and more depends on the density and power of the LED. High voltage strip light because of high voltage, low current, may have less line loss, suitable for long distance, but the working voltage of a single LED may still be low, through the built-in resistor or converter to adapt.
How to distinguish a constant voltage LED strip from a constant current LED strip?
Constant voltage and constant current are two different power drive methods that are suitable for different types of LED strips.
Constant voltage LED strip: requires a stable voltage input; the common voltages are 12V, 24V, and so on. Such a lamp strip is usually designed with resistance to limit the current, as shown by the arrow in the following figure; each small section of the lamp strip is added with resistance, and the size of the resistance value is set according to the current size of the LED that needs to work. Usually the greater the power required, the smaller the resistance value set; on the contrary, the smaller the power of the strip light, the greater the resistance value set.
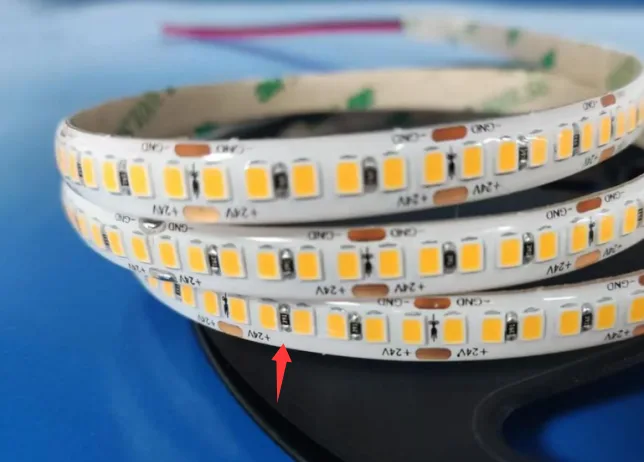
Constant current LED strip: The constant current drive is to keep the current constant, and the voltage changes within a certain range. This type of strip is usually used for high power or where more precise control is required, such as reducing brightness attenuation over long distances. The label of the constant current lamp is generally marked with the current value (such as 500 mA, 1000 mA), and the voltage range may be marked with a certain range, such as 18-36 V. At this time, the power adapter will also have a corresponding constant current output identifier.
Users sometimes pay attention to the product label, the power adapter parameters, the lamp structure (whether there is resistance), and the actual use of the performance, such as whether to support long-distance connection without brightness drop. In addition, constant current lamp strips may require additional constant current drivers, while constant voltage ones are connected directly to the adapter.
As shown in Figure 1 below, the constant current strip light generally has a triode or IC constant current added to each small segment. Figure 2 is in addition to LED; no other electronic components are needed. This is also a constant current strip light, usually having a constant current power supply adaptation. The more the number of groups, the more the required current also needs to increase.
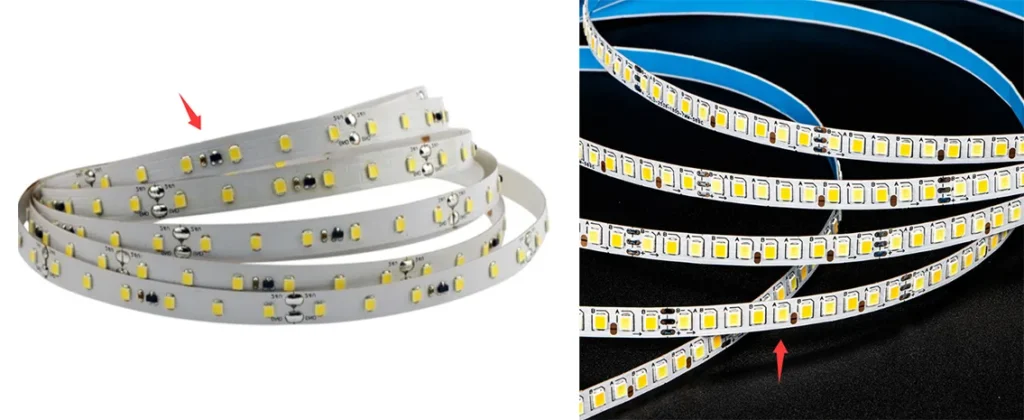
The constant voltage strip needs to match the correct voltage, while the constant current strip needs to match the current and voltage range; otherwise, it may cause damage or poor performance of the LED.
To distinguish the constant voltage strip light and the constant current strip light, you can judge by the following key points:
Appearance: For example, the constant current lamp strip may have no resistance element, while the constant voltage lamp has resistance.
Label: The input voltage of 12V, 24V, and maximum power (such as 12W/m) are marked on the label of the constant voltage lamp. The constant current lamp label will mark the current value (such as 350 mA, 700 mA) and indicate the voltage range (such as 18-24 V).
Voltage drop effect: When the constant voltage LED strip is used for long distances, the end may become dark due to voltage drop.
The constant current strip uses a constant current driver to control the current. It is not affected by voltage drop, and the brightness is uniform for long distances.
Conclusion: The constant voltage lamp can be lit by connecting the power supply of the corresponding voltage. Suitable for short distances, DIY decoration (such as family background light, cabinet light), compatible with ordinary switching power supply, simple installation. Most of the market uses constant voltage lamp strips.
If the constant current strip light is directly connected to the fixed voltage power supply, it may not be bright or damaged. The constant current driver must be used for power supply. Constant current is suitable for long distances, stable brightness, and needs to be paired with a constant current driver, which is a high cost.
What are the waterproof types of the LED strip?
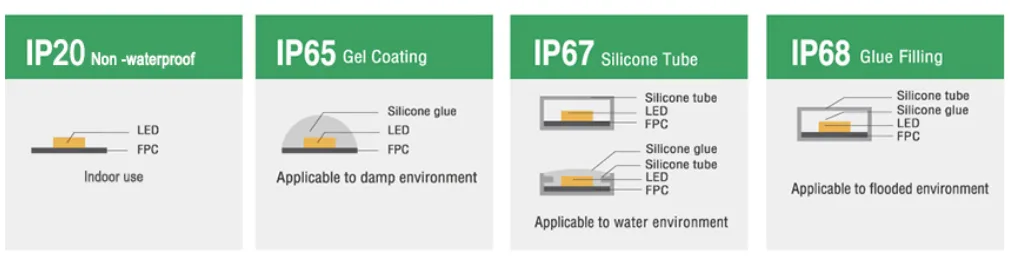
Waterproof LED strip according to the protection level, material and use of different, the current market mainstream as long as there are the next few categories: IP20, IP65, and IP67 are three levels; IP20 is the lowest level, almost not waterproof; At present, our company’s waterproof treatment of light strips mainly includes spraying glue, dropping glue, casing, filling glue, and extrusion technology.
Below I will take you to explore the different structural differences and waterproof performance of the next several waterproof strip lights and see how the following lamps are waterproof.
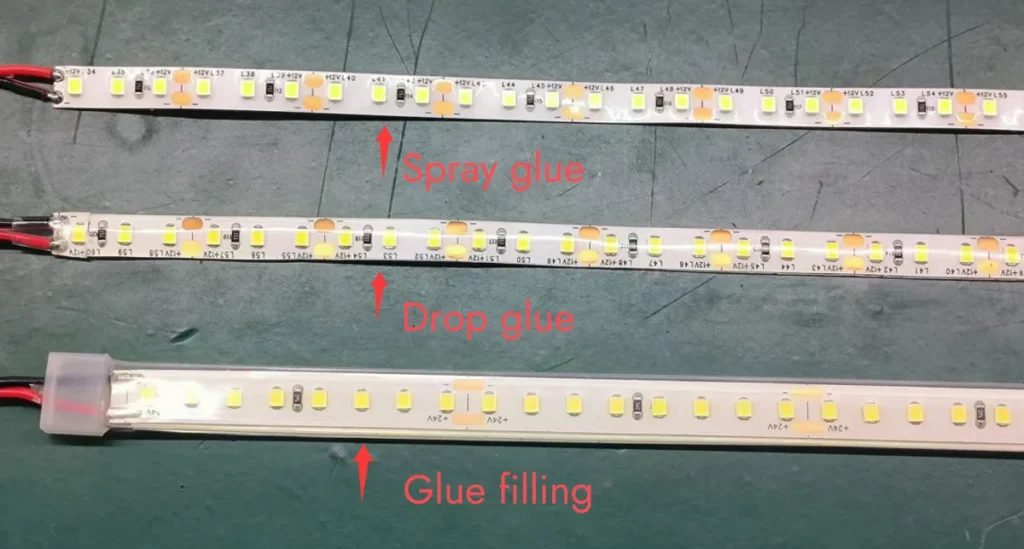
1. Spray glue LED strip
The glue spraying process uses the glue spraying machine to spray silicone glue on the surface of the strip light; the general thickness is relatively thin, and the glue layer is about 30-50 um. The gel acts as a splash-proof.
Spray adhesive light strip is a combination of adhesive process LED lighting products and spray adhesive process light strip products to IP65 or more protection grade for water, dust, or enhanced durability. Dust-proof, moisture-proof, corrosion-proof, and high- and low-temperature resistant.
This light strip is usually installed in bathrooms and kitchens, outside, or anywhere that needs to be waterproof. And any interior areas where the LED strip may be exposed to spraying or splashing water. When the spray LED light is installed where people will come into contact with it, it is easy to wipe the dust from the coating.
2. Casing LED strip
The casing LED strip process is relatively simple, the strip is an external set of silicone hose, good flexibility, suitable for bending installation, but the heat dissipation is slightly poor, and long-term brightness may affect the life. The LED strip light with casing is only suitable for places with high temperatures in the south, and when used in cold areas in the north, the LED will heat up when working in the silicone tube. It’s going to be cold outside, and then the sweaty air and water, and will oxidize resistance PCB, etc.
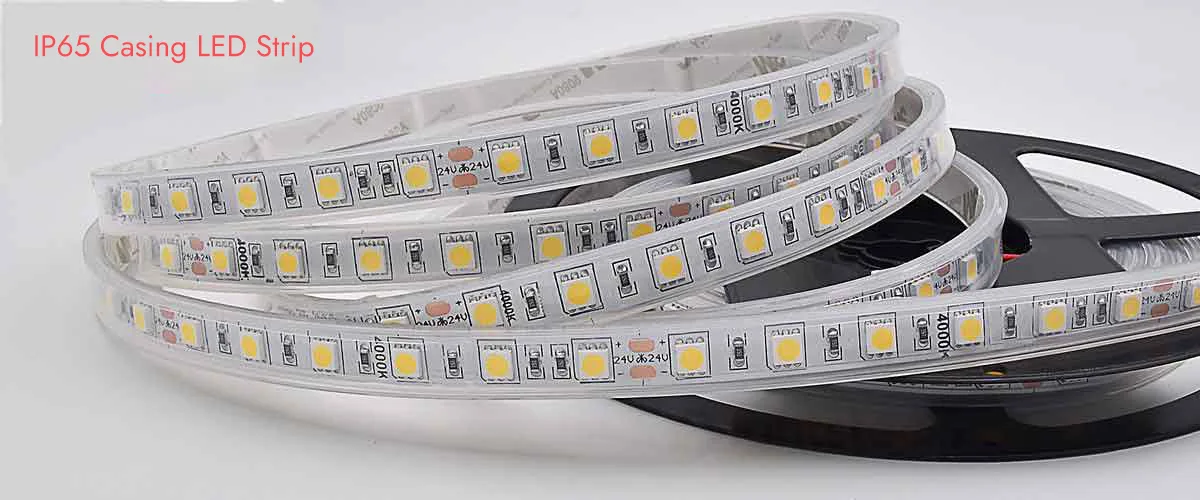
3. Drop glue LED strip
The dropping process begins with surface pretreatment, which enhances the adhesion between the substrate and the silica gel by cleaning, plasma treatment, or coating primer. Then the two-component liquid silica gel is mixed in proportion and vacuumed to eliminate the effect of bubbles on the sealing. Use a high-precision dispensing machine to quantitatively inject glue along the PCB path of the lamp strip to ensure that the thickness of the adhesive layer evenly covers the light-emitting element and circuit. The thickness of the drops is generally controlled at about 2 mm.
The curing time needs to be precisely controlled according to the glue characteristics. The LED strip of the drip glue process reaches the protection level above IP67 while maintaining the flexibility and heat dissipation performance of the LED strip.
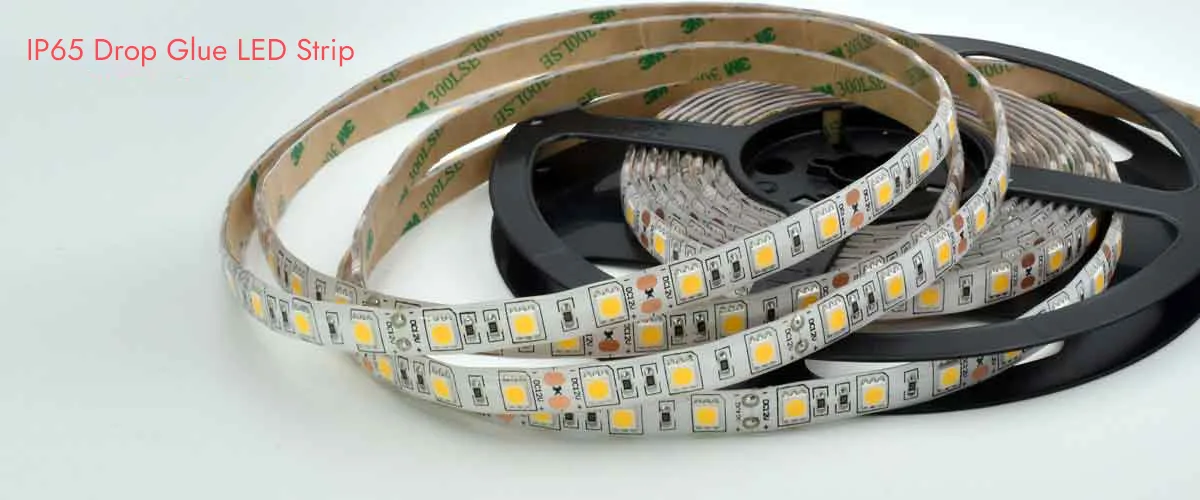
4. Glue-filling LED strip
The LED strip gluing process is to put a set of silicone sleeves on the surface of the LED strip light, and then the two-component organic silicone or epoxy resin is mixed and defoamed in proportion to avoid porosity after curing. The automatic glue filling equipment is used to inject glue at a constant speed along the direction of the strip light, and then the liquid glue (such as silicone, epoxy resin, etc.) is filled into the strip light shell or a specific area to form a sealing layer through curing. Form a flexible and transparent protective layer, effectively improve the waterproof and mechanical strength of the strip light.
After filling the glue treatment, the waterproof grade of the LED strip can reach the IP68 protection level. Can be used outdoors or in harsh environments. Application scenario: swimming pool, fish tank, underwater landscape, and other long-term waterproof environments.
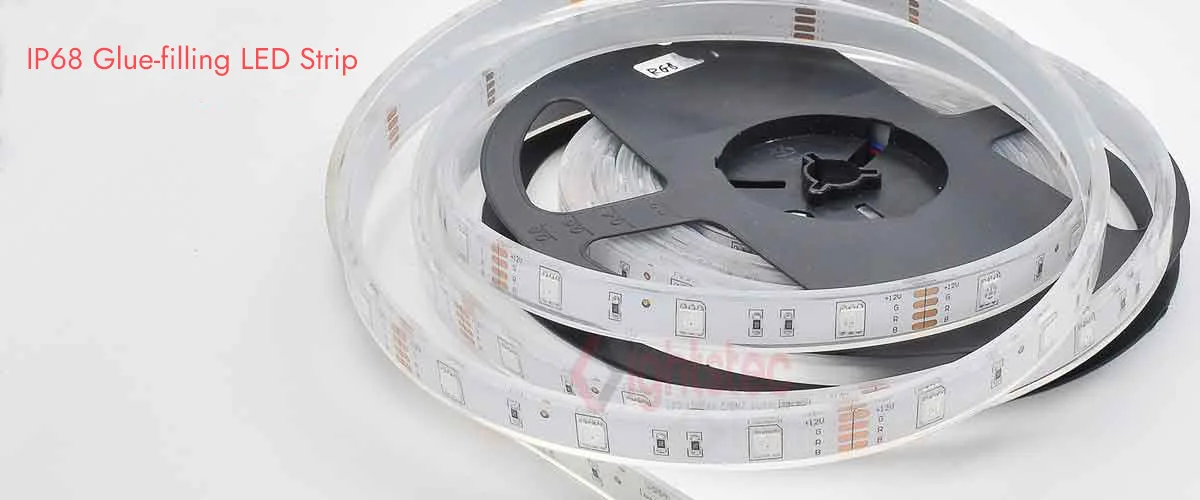
Effect of silica gel on color temperature:
The waterproof silicone material of the drip and filling strips will affect the color temperature of the LED, resulting in an increase in color temperature of about 600-12000K. The following is the test data of the strip light products developed by Signlite Opto-electronics Co., Ltd. For reference:
Test the color temperature comparison between drip glue and filling glue
LED Color Temp | LED/M | Voltage | Current | W/M | lm | lm/W | CRI | Color Tep | Waterproofing Tech | |
2406K | 120 | DC24V | 25MA | 6W | 626.4 | 101.5 | 83.40 | 2373.00 | Bare panel | |
2406K | 120 | DC24V | 25MA | 6W | 569..9 | 95 | 87.60 | 2972.00 | Drop glue | |
2406K | 120 | DC24V | 25MA | 6W | 530.6 | 88.4 | 87.70 | 2977.00 | Glue filling | |
3032K | 128 | DC24V | 31MA | 12W | 1998.9 | 166.58 | 82.10 | 3064K | Bare panel | |
3032K | 128 | DC24V | 31MA | 12W | 1812.9 | 151.07 | 85.60 | 3965K | Drop glue | |
3032K | 128 | DC24V | 31MA | 12W | 1687.3 | 140.6 | 85.40 | 3974K | Glue filling | |
4065K | 120 | DC24V | 25MA | 6W | 662.3 | 110.4 | 82.80 | 4044K | Bare panel | |
4065K | 120 | DC24V | 25MA | 6W | 565.6 | 94.2 | 86.50 | 5710K | Drop glue | |
4065K | 120 | DC24V | 25MA | 6W | 527.9 | 87.9 | 86.20 | 5669K | Glue filling | |
5162K | 120 | DC24V | 25MA | 6W | 700.2 | 116.7 | 83.20 | 4972K | Bare panel | |
5162K | 120 | DC24V | 25MA | 6W | 575.7 | 95.9 | 87.70 | 8287K | Drop glue | |
5162K | 120 | DC24V | 25MA | 6W | 535.7 | 89.2 | 87.50 | 8084K | Glue filling | |
6533K | 120 | DC24V | 25MA | 6W | 679.8 | 113.3 | 83.80 | 6344K | Bare panel | |
6533K | 120 | DC24V | 25MA | 6W | 525.1 | 87.5 | 87.50 | 19162K | Drop glue | |
6533K | 120 | DC24V | 25MA | 6W | 489.3 | 81.5 | 87.30 | 17861K | Glue filling |
5. Extrusion LED strip
The extrusion process of the soft lamp strip is to heat and melt the thermoplastic material (such as PVC, silicone), push it to the precision mold by the screw extruder, and continuously extrude it into a ribbon structure. Synchronously embedded LED lamp bead, wire, and use co-extrusion technology to wrap the protective layer after cooling and forming winding. The process ensures that the strips are flexible, waterproof, and emit even light, making them suitable for curved decorative lighting with high production efficiency and customizable colors and sizes.
The waterproof level of the extrusion lamp can reach IP68 protection level. It can also be used outdoors or in harsh environments. Application scenario: swimming pool, fish tank, underwater landscape, and other long-term waterproof environments.
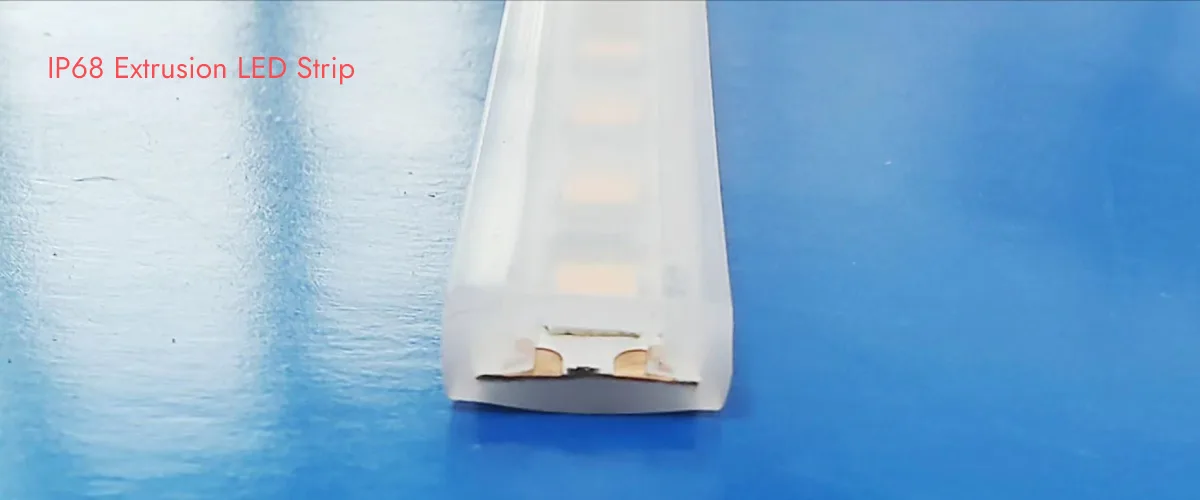
Which is more waterproof, an extrusion LED strip or a filling glue LED strip?
Extrusion LED strips usually adopt a silicone co-extrusion process, with silicone fully covering the bare plate. This process makes the LED strip have excellent waterproof performance; the waterproof level can reach IP68. In contrast, although the waterproof performance of the glue strip is also good, it is usually necessary to fix it by injecting colloids outside or inside the LED strip, and the waterproof effect of this process is relatively weak.
The following is a comparison of the different points of the extrusion and filling LED strip:
Glue-filled LED strip vs. extrusion LED strip
Speciality | Glue-filled LED strip | Extrusion LED strip |
Color temperature drift | High color temperature changes greatly upward | High color temperature changes greatly |
suppleness | Hard after curing, poor bending | Soft and bendable |
IP rating | Usually, high IP ratings ranging from IP67to IP68 | IP68 |
finished cost | About $0.6-0.8/meter | About $0.8-1.0/meter |
Lifetime | Using glue for too long will turn yellow | No yellowing problem |
weight | Increase by about42 grams/meter | Increase by about70grams/meter |
Packaging | Max 10 meters per roll | Typically50meters per roll |
applicable | Kitchen, toilet, outdoor building | Swimming pool, fish tank, underwater view, etc. |
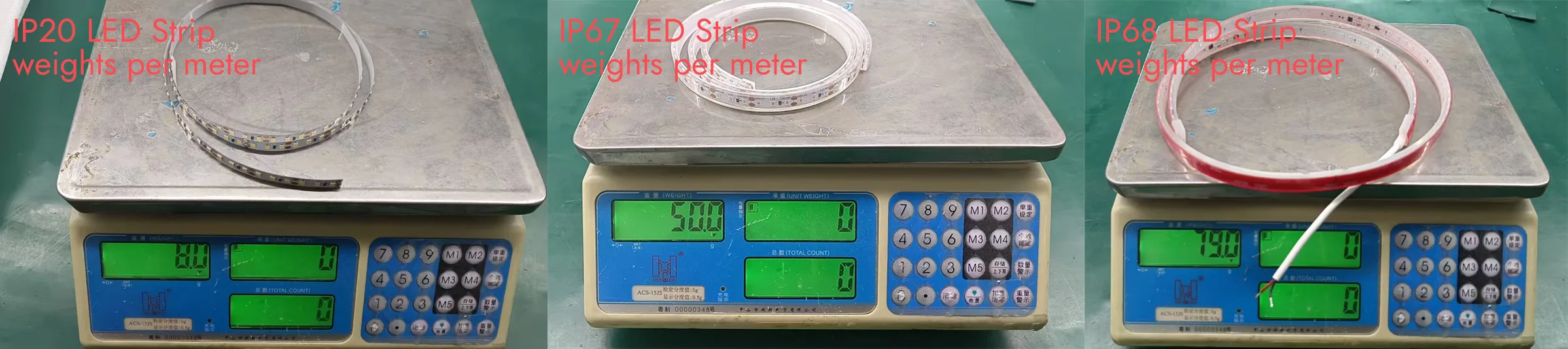
Conclusion: High spraying efficiency, uniform coverage, and general waterproof performance; flexible and accurate, suitable for detail processing, and fast production speed. The sealant has good sealing and strong protection, but the curing is slow and the cost is high. The extrusion strip light has high production efficiency, a regular appearance, and the best water resistance, but the process is complicated and the cost is high.