What is the material of the shell of the LED injection molding module we usually see? What are its characteristics? What is the reason for choosing ABS as the housing for LED injection molding modules?
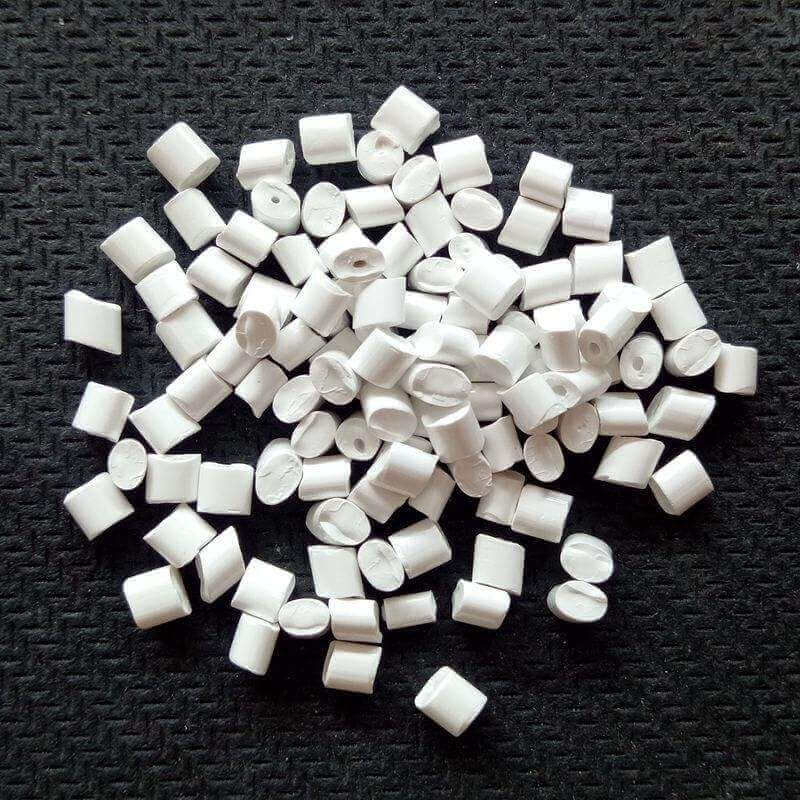
What is the ABS material? ABS material is currently the largest and most widely used polymer. ABS organically unifies the various properties of PS, SAN, and BS, and has excellent mechanical properties of toughness, hardness, and rigid phase balance. In general, ABS is a kind of thermoplastic engineering plastic with a wide range of uses. Next, the editor will introduce the ABS material of the LED injection molding module in detail.
The housing material of the LED injection molding module is ABS, which is one of the five major synthetic resins. It has excellent impact resistance, heat resistance, low temperature resistance, chemical resistance and electrical properties. It also has the advantages of easy processing, stable product size and good surface gloss. It is easy to paint and color, and can also carry out secondary processing such as metal spraying, electroplating, welding, hot pressing and bonding on the surface. It is widely used in industrial fields such as machinery, automobiles, electronic appliances, instrumentation, textiles and construction, is a widely used thermoplastic engineering plastics.
The shell material of the LED injection molding module is ABS, and the appearance is opaque and ivory-colored pellets. The products can be painted in colorful colors and have high gloss. The relative density of ABS is about 1.05, and the water absorption rate is low. ABS has good combination with other materials and is easy to surface printing, coating and plating. The oxygen index of ABS is 18-20. It is a flammable polymer with a yellow flame, black smoke, and a special odor.
The shell material of the LED injection molding module is ABS resin, which is a light yellow solid with certain toughness and a density of about 1.04~1.06 g/cm3. It has strong resistance to acid, alkali and salt corrosion, and can also tolerate organic solvent dissolution to a certain extent. ABS resin can perform normally in the environment of -25 ° C ~ 60 ° C, and has good formability. The processed product has a smooth surface and is easy to dye and electroplate. Therefore, it can be used in household appliances, toys and other daily necessities. The common Lego building blocks are ABS products. ABS resin can be mixed with various resins to form blends, such as PC/ABS, ABS/PVC, PA/ABS, PBT/ABS, etc., to produce new properties and new application fields, such as: mixing ABS resin and PMMA, can be Produced transparent ABS resin.
The shell material of the LED injection molding module is ABS resin, which is currently the largest and most widely used polymer. It organically unifies the various properties of PS, SAN, and BS, and has excellent mechanical properties of toughness, hardness, and rigid phase balance. . ABS is a terpolymer of acrylonitrile, butadiene and styrene, A stands for acrylonitrile, B stands for butadiene, and S stands for styrene.
The shell material of the LED injection molding module, ABS, has good electrical insulation and is hardly affected by temperature, humidity and frequency. It can be used in most environments. It is also a thermoplastic with excellent processing performance and can be processed by general-purpose. It is processed by this method and is widely used in the fields of automobiles, electronic appliances and building materials. The shells of mobile phones are also mostly made of ABS engineering plastics.