The Origin of “Neon Light”
The neon lamp born in 1898 is to inject a rare gas neon gas (neon) into the vacuum glass tube, and then connect the metal electrodes sealed at both ends of the glass tube to a high-voltage power supply, and under the action of a high-voltage electric field, the neon in the tube will be ignited. gas, producing a luminous effect. Therefore, this type of lamp that electrifies the gas and emits light was later named “neon light”.
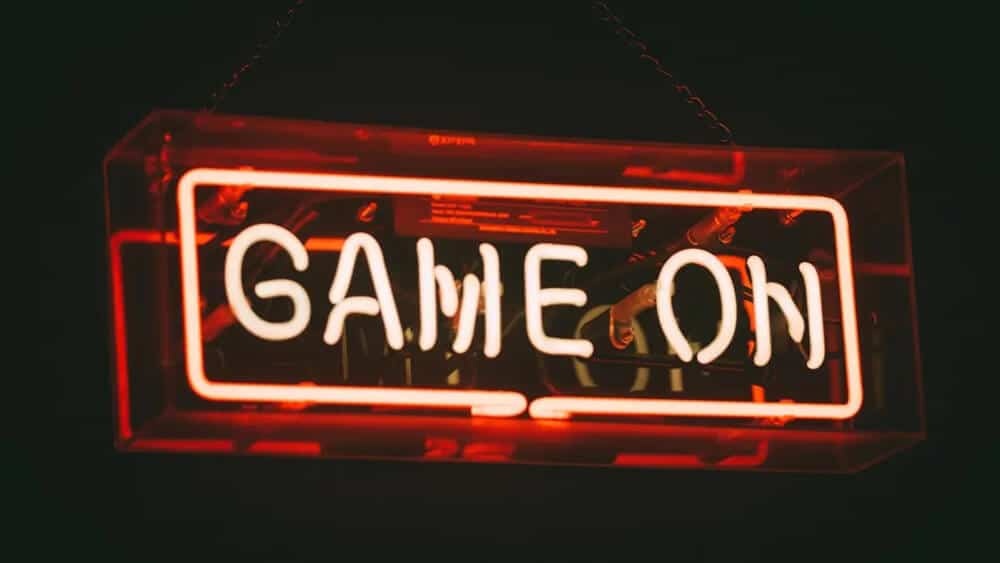
Development path
With the development of LED semiconductor technology, neon lights using LEDs as light sources have gradually replaced traditional neon lights due to their high luminous efficiency, low energy consumption, and high reliability. The material of the lamp body is also replaced by a bendable flexible plastic material from the glass material of the traditional cold cathode tube. The application is simpler, the reliability is higher, and the application field is wider.
LED flexible neon strips using PVC materials were introduced to the market earlier, and have been used up to now relying on their mature technology and price advantages. However, as the market puts forward higher requirements for products and applications, the defects of PVC material characteristics gradually appear. Therefore, a material with better performance – silica gel, has entered this field. After the continuous improvement of technology in recent years, the process of LED silicone neon strips has become increasingly mature and perfect. Its excellent characteristics make it gradually become the current technology to replace PVC neon light strips The mainstream development direction of the market.
Performance analysis of PVC and silicone materials
Aiming at the flexible neon strips using PVC material and silicone material in the current market, the following comparative analysis is made on them from the material itself:
The temperature resistance of PVC material is around -15°C-80°C. The material feels hard and is easily affected by various outdoor factors. The stability of light and heat is poor. After long-term sunlight exposure, it will decompose and produce hydrogen chloride, and further autocatalyze the decomposition. Cause discoloration, physical and mechanical properties also decline rapidly, resulting in hardening, cracking and other phenomena. It is not suitable for extremely humid places with acid, alkali and salt corrosion. In addition, the burning of PVC will produce irritating toxic gases.
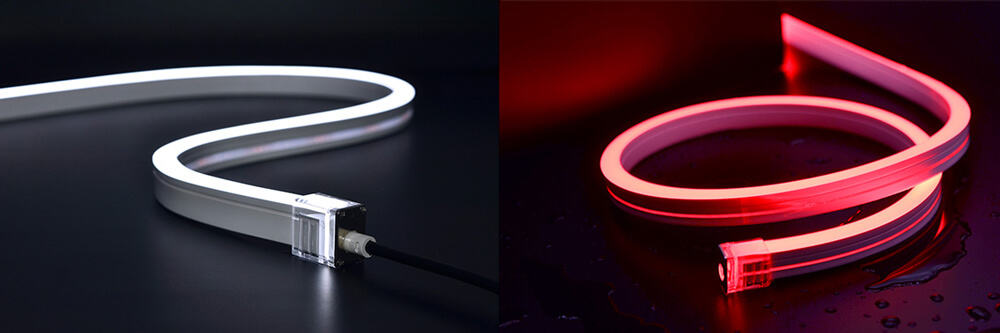
Compared with PVC material, silicone material has the following advantages:
- Excellent weather resistance: The material has good thermal stability and can maintain a normal soft state for a long time under the environment of -50°C-150°C without embrittlement, deformation, softening, aging, etc.
- Excellent UV resistance: It can be exposed to strong sunlight for a long time (more than 5 years) without yellowing and aging, and can be used in outdoor environments for a long time.
- Excellent corrosion resistance: Silica gel has stable chemical properties, does not react with any substance except strong alkali and hydrofluoric acid, and can resist the corrosion of ordinary acids, alkalis and salts. Yacht environment or facilities.
- Excellent light transmittance: Applied to the light strip, the light loss to the light strip can be reduced to a lower level.
- Excellent tear resistance: Excellent tear resistance, good physical and mechanical properties, after the silicone is molded, it can withstand any manual tearing, and the silicone will not be damaged or deformed (it will fully rebound after being pulled).
- Good thermal conductivity: Extruded silicone has a thermal conductivity of 27W/MK, while PVC has a thermal conductivity of 0.14W/MK, which can effectively dissipate heat when applied to light strips.
It can be seen that in the future LED flexible neon strip products, silicone materials will occupy a dominant position with its outstanding comprehensive performance.