Whenever the night twilight descends, the LED strip light in the night flows out of the trajectory of the river of stars, window-dropping stars, and treetops winding between such as thousands of meteors crossing, and the building’s wall screen color changes in thousands of colors. The light band softly spills down, gently wrapping every corner, so that the evening breeze brings a romantic color.
Friends! Have you ever wondered how they produce those LED strip lights that shine beautifully at night? Are you curious about the design and production process of LED strip lights, or would you like to know the manufacturing details, such as DIY or reference when buying? Today, I’m going to tell you more about this interesting LED strip light design and manufacturing process.
What raw materials are LED strip lights made up of?
The raw materials for the production of LED flexible light strips mainly include LED beads, PCB boards, wires, tapes, and so on. Among them, LED is the heart of the strip; the quality of the LED directly determines the brightness and life of the strip. The circuit board is like the blood vessels of the strip, responsible for transmitting power to the LED; wire is the current from the controller to the LED medium; tape is like the protector of the strip and can be firmly fixed to the strip to ensure that the LED strip installation is solid.
About LED lamp beads and tape, my last article has a detailed introduction; interested friends can click to understand.
How to Choose the Right LED for LED Strip Lights
How to judge and choose the quality of led light strip adhesive tape?
What is an LED strip light PCB?
Here we come to understand another important material for LED strip lights: PCB boards.
A PCB board for an LED strip light is a flexible circuit board, also called an FPC circuit board (flexible printed circuit), which is a kind of circuit board made of flexible material with the characteristics of being bendable, lightweight, high-density wiring, and so on. It can be bent, curled, and adapted to complex space layouts.
The main constituent materials of FPC include substrate, conductive material, adhesive, and cover film. Each material plays an important role in the performance and function of FPC to meet the needs of different circuit designs. The following are the common layers of FPC:
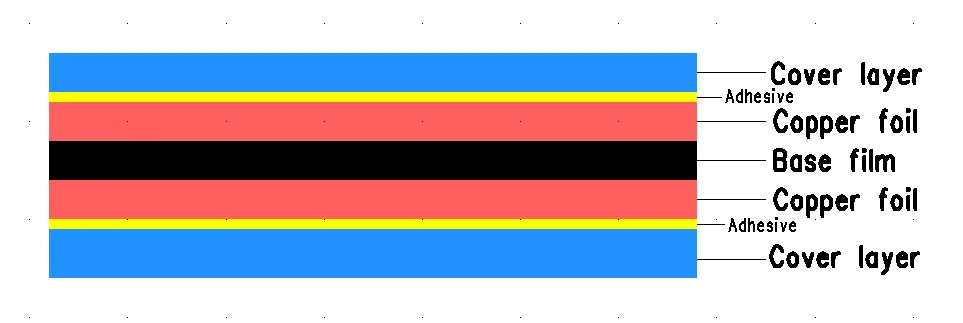
1. Base layer (Base Film): Usually polyimide (polyimide, referred to as PI) or polyester (polyester, referred to as PET), the thickness specification of 1/2mil, 1mil, and 2mil is commonly used; 1/2mil and 1 mil are commonly used.
2. Copper foil layer (Copper Foil): calendered copper (RA Copper) and electrolytic copper (ED Copper) are two kinds of thickness specifications for 1/3 oz, 1/2 oz, 1 oz, etc. Calendered copper (RA) is made of copper plate; after many repeated rolls, its crystallization is flaky in organization, and electrolytic copper (ED) is made through a special electrolysis machine in the round cathode drum in continuous production. In general, the FPC needs dynamic bending selection of calendered copper (RA); the FPC only needs 3-5 times bending (assembly bending) selection of electrolytic copper (ED). Electrolytic copper for the conductive properties and cost advantage; most of the current light boards use electrolytic copper.
3. Adhesives: epoxy resin, used to bond the copper foil to the substrate, providing strength and durability; acrylate adhesives, used in some special applications, to provide better flexibility and chemical resistance.
4. Cover Layer: the same material as the base layer, insulation, solder resist, and protection; commonly used thickness of 0.5mil.
How to choose a PCB board for an LED strip light?
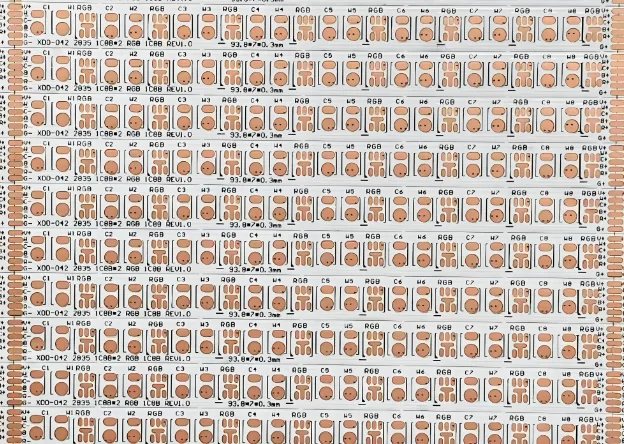
The PCB board of the LED strip light has single and double panels; the single panel usually has two thicknesses of 0.07 mm and 0.11 mm. It should be noted that, if the use of white cover film, the thickness of the single panel will increase by 18 um; double-sided boards usually have three thicknesses of 0.11 mm, 0.12 mm, and 0.2 mm. Similarly, if a white overlay film is used, the thickness of a double-sided board increases by 36 um. In some special applications or high-end products, the thickness of the FPC may reach between 0.3 mm and 0.55 mm to meet higher mechanical properties, electrical properties, or thermal management requirements.
The copper thickness of a PCB usually refers to the thickness of the copper layer of the laminate, which is generally expressed in ounces per square foot (oz), such as 1 oz, 2 oz, etc. If the copper thickness increases, the electrical conductivity should be better, and the current-carrying capacity is also stronger, but copper itself is a precious metal. 2 oz of copper thickness is more expensive than 1 oz because twice the amount of copper is used; the cost will rise.
The copper thickness of the PCB affects the price of the light board. If the PCB of an LED strip light needs to carry a higher current, for example, power 20 W/m, it may need 2 oz of thick copper to reduce heat and improve efficiency. 1oz copper thickness single panel price is about 0.07 USD/square decimeter; 2oz copper thickness may increase to 0.11-0.14 USD (material + processing fee increase of about 60-100%). Copper thickness increases every 1 oz, then the cost of LED strip PCB may rise 30%-50%.
Although the copper thickness increases the cost, it may be a necessary design choice. If the design does not require thick copper, the use of thick copper is a waste of cost, so the design needs to be combined with the electrical performance, heat dissipation needs, and budget decisions. Currently more PCB boards are used in double-sided boards; single-panel is only applicable to occasions where the brightness is not high and the distance is short; the market share of the use of very little is double-sided boards; double-sided boards are relatively high-priced but more widely used.
How is an LED strip light designed with LED series-parallel combinations?
LED light strips have different LED densities and usually have different numbers of LEDs per meter, which will have different string and parallel combinations. For example, SignliteLED produces strips with 60 LEDs/meter, 128 LEDs/meter, and 140 LEDs/meter. Here we take 60 LEDs/meter as an example to see how LEDs are set up in series-parallel combinations. First of all, the power supply voltage is different; it will have a different series-parallel relationship, a 12V power supply strip, and a series-parallel combination of 3 series 20s; if it is a 24V power supply, the series-parallel relationship is 6 series 10s.
Example: Assuming that the Vf value of the LED is 3V, as shown in Figure 1 below is a 12V power supply circuit, the series-parallel relationship is 3 series and 2 parallel; after connecting 3 LEDs in series, the total voltage of the LEDs in series will be 3V×3 = 9V. The remaining 12V – 9V = 3V is divided by the current-limiting resistor R to ensure that the LEDs work stably and to avoid over-voltage damage. Note that if the number of LEDs in a single string is too large (e.g., 4 in series need 12V), it may lead to no voltage margin for the current limiting resistor, affecting the brightness control.
Figure 2 below is a 24V power supply circuit; the relationship between series and parallel is 6 series and 2 parallel. After connecting 6 LEDs in series, the total voltage of the LEDs in series is 3V × 6 = 18V. The remaining 24V – 18V = 6V is divided by the current-limiting resistor R. Then, by adjusting the size of the resistor R, the voltage is divided by the current-limiting resistor. Then, by adjusting the size of the resistor R value, the current of the LEDs can be changed, thus changing the brightness of the LEDs.
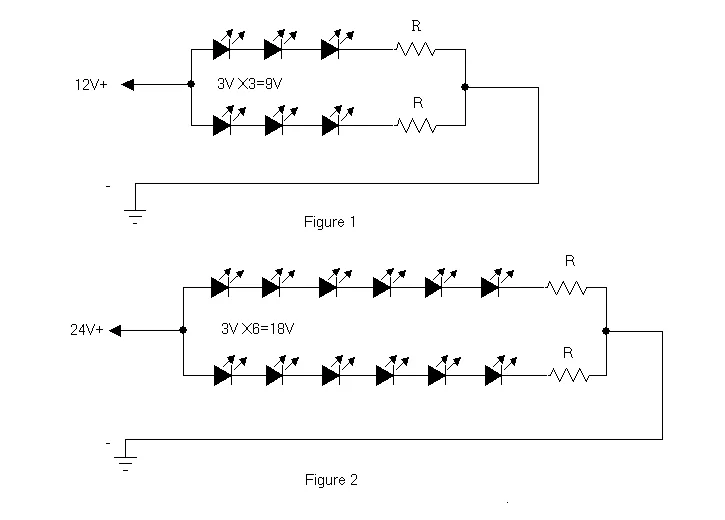
How to calculate the resistance of LED strip lights?
In LED strip lights, the correct choice of resistance is crucial. Ohm’s law (V=IR) is the basic law for calculating resistance. As shown in the diagram below: If we use a 24 volt power supply and each LED requires 3V, then the voltage requirement for a total of 6 LEDs is 18V. Therefore, the voltage across the resistor should be 24V – 18V = 6V. If the current flowing through the circuit is 0.03 Amps, then according to Ohm’s Law, the resistance value is 6V ÷ 0.03A = 200 Ohms.

Another noteworthy issue is the need to consider the power of the resistor to withstand the power formula: P = UI; the resistor’s supply voltage in the above diagram is 6V. If the current flowing through the resistor is 0.03A, then the resistor’s power is calculated as follows: 6V×0.03A = 0.18W. Then we select the chip resistor, which must be greater than 0.18W, after checking the resistor value of 0805, which is 0.125W, while the resistor value of 1206 packages is 0.125W. And a 1206 package resistance value of 0.25W; if the choice of 0805 package resistance value is obviously small, then we need to choose the 1206 package resistance. This design resistor can ensure the stability of the current and the resistance of the long-term work of reliability.
Selecting the correct resistance value can ensure the safe operation of the LED strip to avoid overheating or damage. If the resistor value is too large, it may lead to too little current, and the LED may not be normal light; while if the resistor value is too small, it may lead to too much current, triggering safety issues.
It is worth noting that the actual application may need to consider more factors, such as the effect of temperature changes on the resistance value, the power of the LED, and other factors. Therefore, in practical applications, it is recommended to select the appropriate resistance value according to the specific needs and carry out the necessary tests and adjustments.
In addition, a reasonable choice of resistance can also optimize the performance of the circuit. For example, by adjusting the resistor value, the brightness of the LED can be changed. In some cases, it may be necessary to connect multiple resistors in parallel to spread the current to ensure the stability and reliability of the circuit.
In short, correctly calculating and selecting the right resistor value is critical to the proper operation of LED strip lights. Understanding and applying Ohm’s law can help us better control the circuit and ensure the safe and efficient operation of LED strip lights.
Why are there a different number of LEDs in LED strip lights?
Now on the market, the number of LEDs per meter is different; common specifications are 60, 120, 180, and 240 LEDs per meter. Why are there so many kinds? The main reason is that different customers have different brightness requirements, which include application scenarios, energy consumption, heat dissipation, cost control, and installation effect, etc. The higher the number of LEDs, the higher the brightness should be per unit area.
For example, decorative LED strip lights may not need too high a density; use 60 LEDs per meter to meet it, while functional lighting may require 180 LEDs per meter or higher density. Commercial premises may need to use high-density strip lights to create an atmosphere, while the general family may find a medium density of 120 LEDs per meter is enough.
In addition, the cutting interval may affect the number of lamp beads in the design. The same is 60 LEDs per meter, assuming that every 3 LEDs or 6 LEDs are a cutting point. The length of the two cutting points is not the same; 3 LEDs as a group have a cutting distance of 50 mm, and 6 LEDs as a group have a cutting distance of 100 mm.
Cost is also a factor. More LEDs mean more material cost, and the price may be higher. Different LED densities of light strips to meet different budget consumers. Low density (60 LEDs per meter) is suitable for users with limited budgets, while high density (180 LEDs per meter) is suitable for users who are looking for effect.
The more LEDs, the higher the power may be; the power consumption and heat will increase, so you need to pay attention to the design. A high-density LED strip may need a better heat dissipation design; otherwise, it will affect the service life of the strip.
Installation effect: LED density is high; the light is more continuous and uniform to avoid the emergence of obvious dark areas or light intervals. This is important in places where smooth light effects are needed, such as TV backdrops or display cabinets. And a low-density LED strip may be more flexible in bending installation because the LED spacing is large, and bending is not easy to appear extrusion pressure concentration, such as an S-shaped LED strip.
In addition to buying an LED strip light, you need to synchronize the power of the strip (such as 10W or 20W per meter); high-density strip lights may require higher power supply support.
How to improve the luminous efficiency of an LED strip light?
To improve the luminous efficacy of LED strip lights, the most direct way is to purchase higher brightness LEDs or increase the number of LEDs, but the result is that the cost will also increase more accordingly; after all, the price of high brightness LEDs will be much higher. Usually an LED brightness of 26-28 lm SMD2835 has a price of about 0.0025 USD. If you use 30-32 lm LEDs, the price will be 0.0035 USD. According to the 1-meter with 120 LED calculation, the 1-meter light strip cost increased by 0.12 USD.
Another way to increase the light efficiency is to appropriately increase the number of LEDs in series to reduce the power lost in the resistance. This method relatively improves the efficiency, and the cost does not increase too much.
1. Assuming that there are 120 LEDs with 10W power per meter and a voltage of 24V, and 6 LEDs for a group, then 1 meter of LEDs for 6 series of 20 and each group of LEDs has a current of 10 ÷ 24V ÷ 20 = 0.021A. Looking up the table below the LEDs, the Vf value = 2.77V. We calculated that the voltage value of its resistor is 24V – 2.77V × 6 = 7.38V. Which is consumed in a single resistor on the useless power of 7.38V × 0.021 = 0.155W; all the resistors consume the total useless power of 0.155W × 20 = 3.1W; 3.1 ÷ 10 × 100% = 31%. This results in the luminous efficiency of the LED strip being 69%.
2. Let’s look at the 120 LEDs 10W per meter to change the efficiency of the number of series: 8 LEDs for a group, then the circuit of the series for the 8 series 15 and each group of lamp beads current: 10 ÷ 24 ÷ 15 = 0.028A; check the table below. 28 mA corresponding to the value of the Vf = 2.8 V, we calculated the value of the resistor voltage: 24V – 2.8V × 8 = 1.6V, which is consumed in the resistor on the useless power: 1.6V × 0.028 = 0.045W. All the resistors consumed by the total useless power are 0.045 × 15 = 0.675W, consumed in the resistor on the power ratio: 0.675 ÷ 10 × 100% = 6.75%, resulting in the light-emitting efficiency of the strip being 93.25%.
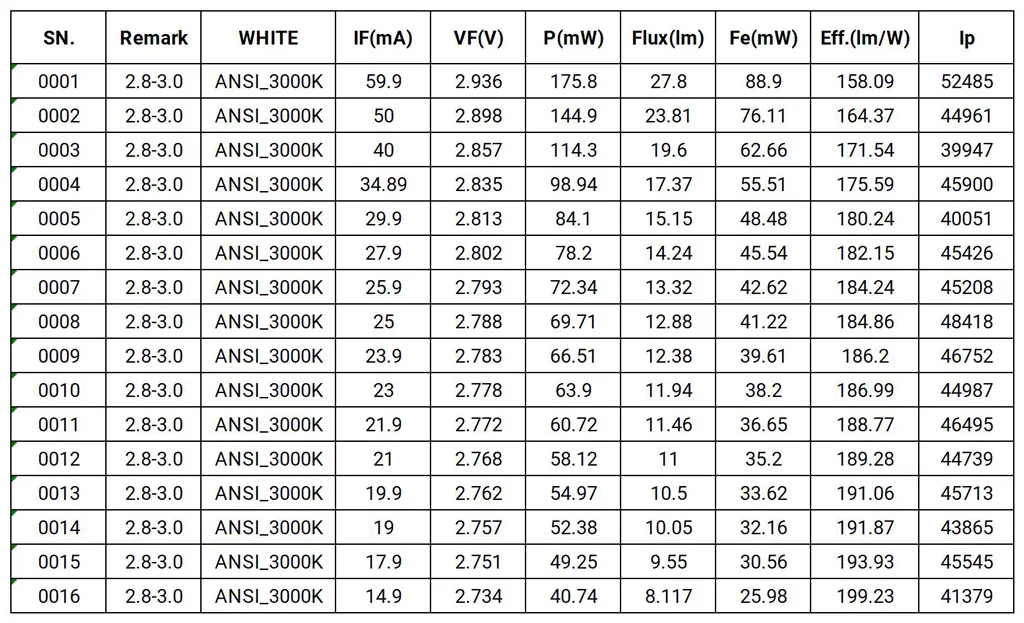
From the above two sets of calculations, it can be seen that 8 LEDs in series are more efficient than 6 LEDs in series; efficiency increased by about 25%, and multi-LED series light efficiency increased. But there is a problem to be noted, that is, to consider the LED strip voltage drop problem. LED must be selected with a small Vf value so as to ensure that after a long distance there is enough voltage margin for the LED to work properly. In addition, with the use of this multi-LED series with a length of 5 meters, it is best to increase the complementary power. Otherwise, it will lead to no voltage margin on the current limiting resistor, affecting the brightness of the back end of the strip.
High luminous efficacy LED strip lights with energy saving, long life, high brightness, environmental protection, and flexible design advantages have become the mainstream choice of modern lighting, especially suitable for the pursuit of high efficiency, aesthetics, and sustainability for the user.
SignliteLED has been committed to improving the luminous efficacy of the LED strip light. 128 LEDs/m is the development of our customers with high luminous LED strips. Compared with the similar 120 lm/m in the market, the luminous efficiency reaches 180 lm/w; the luminous efficiency has been effectively improved by about 25%, which is one of the best-selling products at present.
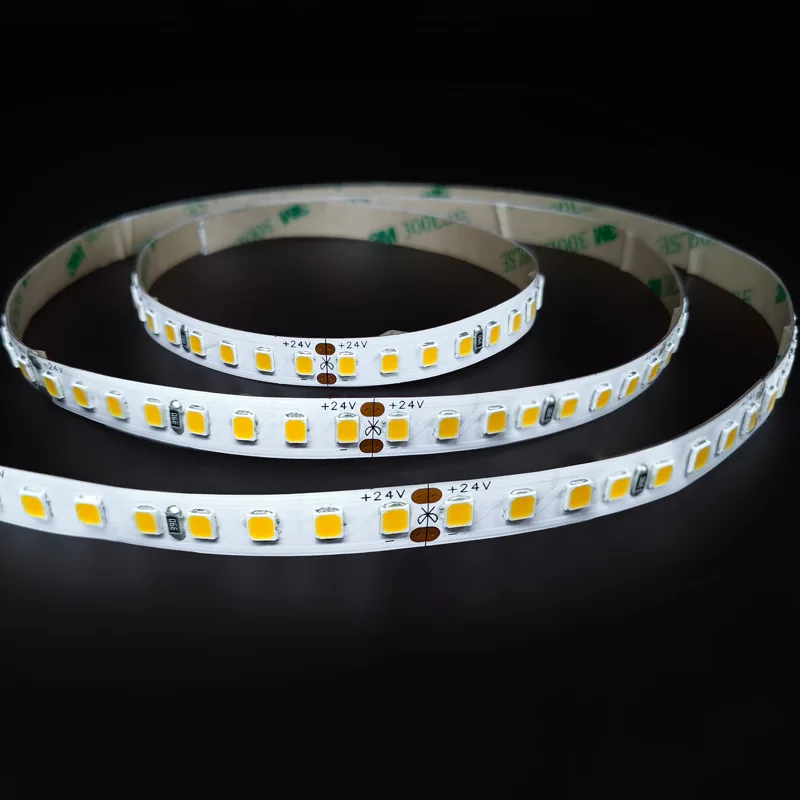
High Efficiency 128LEDs/m SMD2835 LED Strip Light
Model: FQX10T128C
LED Type: SMD2835
LED QTY per Meter: 128
PCB Width: 10mm
Color Temperature: 2700K/3000K/4000K/5000K/6500K
Input Voltage: DC24V
Power per Meter: 12W
Cutting Unit: 62.5mm/8LEDs
IP Grade: IP20/IP54/IP65/IP67/IP68
Warranty: 5 years
Price: USD $1.67/meter
How are LED Strip Lights Manufactured?
The manufacturing of LED Strip Lights is a delicate process, watch our LED Strip Lights Manufacturing video to understand the entire LED Strip Lights manufacturing process.

What is the appropriate working temperature of an LED strip light’s LED?
In daily use, the surface temperature of an LED strip light is not hot (about 50℃ or less) as a reference standard. If the temperature is too high, you need to troubleshoot the heat dissipation conditions or reduce the intensity of use. An LED strip with a working temperature between 40 ℃ and 60 ℃ is appropriate; this range is based on the strip’s internal electronic components and materials set by the temperature resistance so as to ensure that the strip works stably and maintains a good lighting effect and service life.
Factors affecting the temperature of the LED strip
Power and brightness: The power and brightness of the LED strip light will directly affect its operating temperature. The higher the power, the greater the brightness of the strip, and the heat generated at work will increase accordingly.
Use of the environment: the use of the LED strip light environment will also have an impact on its temperature. Using the strip in a closed or poorly ventilated space is likely to lead to heat buildup, which will increase the temperature.
Installation: The installation method of the LED strip light and the design of the heat dissipation system are also important factors affecting the temperature. Reasonable installation and wiring can ensure even heat dissipation of the strip and avoid excessive bending or folding of the strip so as not to affect its thermal performance.
Excessive temperature will lead to accelerated light decay and shorten the life of the LED strip. LED junction temperature (chip temperature) generally does not exceed 85 ℃ ~ 105 ℃ (specific to the manufacturer’s specifications shall prevail); high temperatures will accelerate the light decay. The life of the LED is usually related to the temperature; for every 10℃, the life of the LED may be correspondingly reduced by 10%. So it is very important to control the temperature within a reasonable range. Manufacturers generally give the maximum operating temperature; for example, some LED strips may be labeled with a maximum of 60°C or 70°C, but in practice it is recommended not to exceed 55°C to maintain stability and life.
The following chart is a set of LED temperature and life test data for reference:
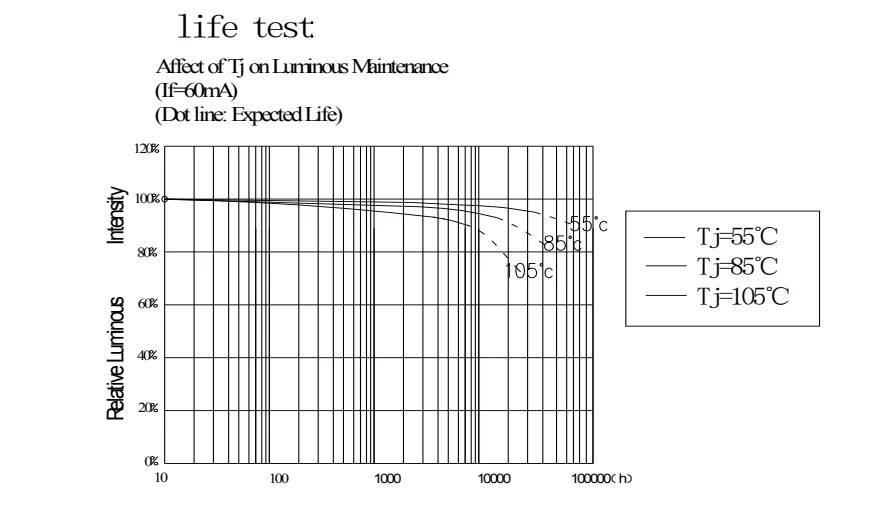
LED light strips: Try to avoid using them in confined or high-temperature environments. If it is outdoors, ambient temperature variations may also have to be considered. Better heat dissipation measures are needed, and the installation is paired with aluminum profile heat sinks; Also note that LED strip lights may be a safety hazard if they are installed near flammable materials with high temperatures, and this is when you need to ensure that the heat dissipation and the installation location are safe.
To effectively reduce the temperature of the lamp bead, the power settings should be reasonable; with high-power lamp bead working current, the temperature will also rise. So the working current of the lamp bead is strictly controlled to within 30 mA, which is the most ideal. In addition to choosing 2OZ thick copper above the LED strip, the heat dissipation effect will also be strengthened.
Summary
The flexible LED strip production process is relatively simple, but each of these links is very important and needs to be strictly controlled only through a strict production process in order to produce good quality LED strips to meet consumer demand. Fine management of the LED strip production process is to achieve high reliability and low-cost mass production of the core of the product, which directly affects the competitiveness of enterprises in the market.