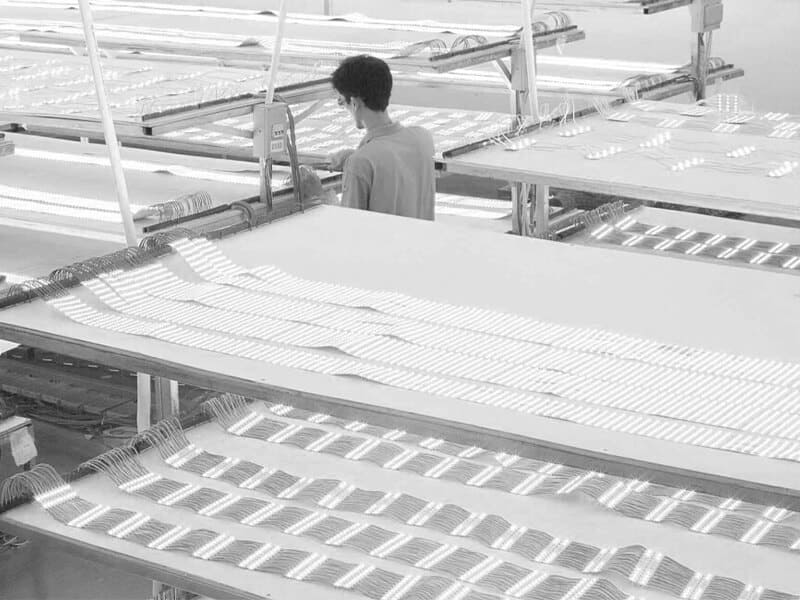
There will inevitably be some problems in the production process of LED flexible strips. Today, I will briefly summarize the common problems.
One. Bubbles appear in the glue during the production of LED flexible strips. The main reason is that the operation time of the glue is too long, the amount of glue is too large, the mixing method is incorrect, there is no vacuum degassing or the degassing time is too short.
1. The glue operation time is too long: the longer the epoxy AB glue or polyurethane glue is placed after mixing, the viscosity of the glue will become thicker and thicker. When the glue thickens, the air bubbles will be difficult to discharge. Solution: shorten the operation time (divided into: dispensing time, vacuuming time, parking time, and using time when dispensing glue).
2. The amount of glue used: when the ambient temperature of epoxy resin glue or polyurethane glue is constant, the larger the amount of glue mixed at one time, the faster the curing speed will be. If the amount of glue is too much, the viscosity of the glue will gradually increase as time goes on, and the glue will become more viscous, which is relatively difficult to discharge air bubbles. Solution: It is recommended to use a little less glue, which is more suitable for 200G/200G. If you want to mix more, it is recommended to divide the glue into 2-4 cups after stirring evenly for defoaming and vacuuming (principle: the larger the volume, the faster the curing speed). If you do not divide it, the viscosity of the glue will thicken in a short time. Finally, the air bubbles are difficult to discharge.
3. The stirring method is incorrect: the solution is to stir clockwise. Because stirring clockwise and stirring counterclockwise is more likely to produce air bubbles.
4. Be sure to defoam (vacuum machine), the recommended defoaming time is 6-8 minutes.
Two. The surface of the glue does not dry during the production of LED flexible strips. The main reason is that the glue ratio is not accurate or the mixing is not uniform enough.
1. The glue ratio is inaccurate: when the ratio is inaccurate, part of the glue will not be able to react chemically, and if there is no reaction, it will not be fully cured, so it will not dry or be very sticky. Solution: The error range of glue mixing should be controlled within 1%-1.5%.
2. Uneven glue mixing: Uneven mixing will cause the surface to dry out, partly dry out or the curing time will become longer. Solution: During the stirring process, be sure to stir the surrounding and bottom of the container in place. The recommended stirring time is 5-6 minutes.
Three. Phenomena and explanations after the glue is cured.
1. If the epoxy glue is placed in water for a long time, the surface will turn white, but after taking it out, it can be restored to its original state after 5 hours at room temperature. Polyurethane glue is not easy to turn white when placed in water.
2. About the bonding performance of glue, silica gel and PVC: Silicone material and PVC are materials that are difficult to bond. Epoxy resin glue has a certain bonding force to PVC, but the bonding performance with silicone material is not good, and it is easy to bond with silicone u-shaped sleeve breaks away.
3. After the glue is basically cured, the surface will look a little sticky, so don’t reel and pack it after 24 hours. If it is packed after 24 hours, the surface is prone to sticky hands and easy to break, because after 24 hours, the glue is in a basically cured state and has not been completely cured. Solution: It is recommended to reel and pack after 48 hours.
4. The main reasons for the cracking of the glue on the SMD lamp of the light strip are: inaccurate glue mixing or uneven mixing, resulting in incomplete curing of the glue, and insufficient coating on the surface of the light strip.